A Comprehensive Guide to the Refine and Advantages of Plastic Extrusion
In the huge world of production, plastic extrusion emerges as a highly efficient and crucial process. Altering raw plastic right into continuous profiles, it provides to a plethora of sectors with its amazing convenience.
Understanding the Fundamentals of Plastic Extrusion
While it may show up complex at initial glimpse, the process of plastic extrusion is essentially easy. The process begins with the feeding of plastic material, in the type of pellets, powders, or granules, into a warmed barrel. The designed plastic is after that cooled, strengthened, and reduced into wanted lengths, completing the procedure.
The Technical Refine of Plastic Extrusion Explained
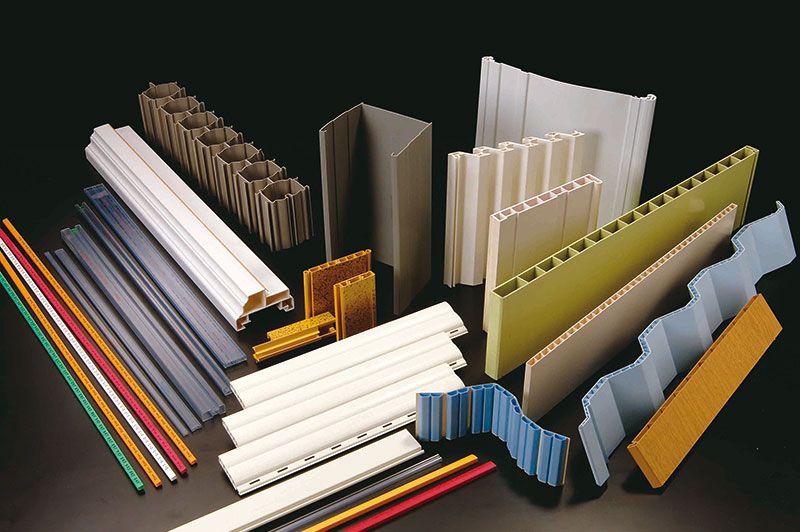
Kinds Of Plastic Suitable for Extrusion
The selection of the appropriate kind of plastic is a crucial aspect of the extrusion process. Numerous plastics offer distinct buildings, making them more matched to particular applications. Polyethylene, for instance, is typically utilized due to its reduced expense and very easy formability. It provides excellent resistance to chemicals and dampness, making it optimal for items like tubing and containers. In a similar way, polypropylene is an additional prominent choice due to its high melting factor and resistance to fatigue. For more robust applications, polystyrene and PVC (polyvinyl chloride) are typically selected for their strength and longevity. Although these are typical options, the choice inevitably depends on the particular needs of the item being generated. So, comprehending these plastic types can substantially boost the extrusion process.
Contrasting Plastic Extrusion to Various Other Plastic Forming Methods
Understanding the kinds of plastic suitable for extrusion paves the method for a wider conversation on how plastic extrusion compares to various other plastic creating techniques. These include injection molding, impact molding, and thermoforming. Each approach has its unique uses and advantages. Injection molding, as an example, is superb for creating detailed parts, while blow molding is excellent for hollow objects like bottles. Thermoforming excels at developing huge or superficial parts. Plastic extrusion is unequaled when it comes to creating constant profiles, such as gaskets, pipelines, and seals. It also permits for a regular cross-section along the length of the product. Therefore, the selection of technique greatly why not try these out relies on the end-product needs and specs.
Key Benefits of Plastic Extrusion in Production
In the world of manufacturing, plastic extrusion provides several substantial benefits. One noteworthy benefit is the cost-effectiveness of the procedure, which makes it a financially appealing manufacturing approach. Additionally, this technique supplies remarkable product adaptability and enhanced manufacturing speed, therefore raising general production performance.
Affordable Production Approach
Plastic extrusion jumps to the center as an affordable production approach in manufacturing. This process attracts attention for its ability to produce high volumes of material rapidly and successfully, giving makers with significant cost savings. The key price advantage is the capacity to use cheaper resources. Extrusion makes use of polycarbonate materials, which are less pricey compared to metals or porcelains. Additionally, the extrusion procedure itself is relatively easy, decreasing labor prices. Additionally, plastic extrusion calls for less power than traditional manufacturing techniques, adding to reduced operational costs. The procedure additionally lessens waste, as any faulty or excess materials can be reused and reused, supplying one more layer of cost-effectiveness. Overall, the monetary advantages make plastic extrusion a highly attractive choice in the production sector.
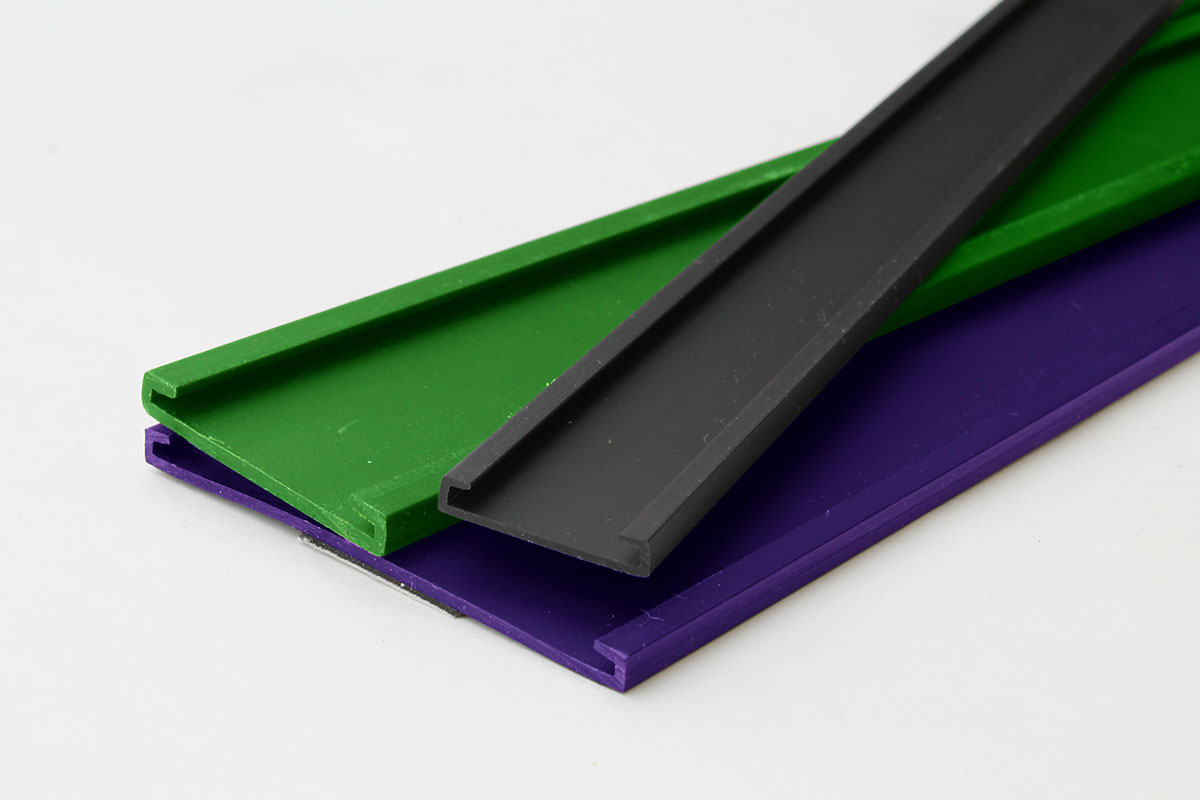
Superior Item Flexibility
Past the cost-effectiveness of plastic extrusion, an additional significant benefit in making depend on its remarkable item versatility. This procedure allows for the development of a large array of go right here items with differing styles, shapes, and dimensions, from simple plastic sheets to intricate accounts. The flexibility is credited to the extrusion pass away, which can be personalized to produce the wanted item style. This makes plastic extrusion a perfect remedy for industries that call for customized plastic parts, such as automotive, construction, and packaging. The ability to produce diverse items is not just advantageous in meeting details market needs but also in allowing manufacturers to discover new line of product with marginal capital expense. Fundamentally, plastic extrusion's product versatility cultivates advancement while improving functional performance.
Boosted Manufacturing Speed
A considerable advantage of plastic extrusion depends on its improved production speed. This manufacturing procedure enables high-volume manufacturing in a fairly brief time period. It can creating long, constant plastic profiles, which considerably reduces the production time. This high-speed production is specifically useful in industries where large quantities of plastic components are needed within tight target dates. Few various other production procedures can match the speed of plastic extrusion. In addition, the ability to maintain constant high-speed production without sacrificing product high quality establishes plastic extrusion besides various other techniques. The enhanced production speed, therefore, not only allows producers to meet high-demand orders however likewise adds to enhanced efficiency and cost-effectiveness. This beneficial feature of plastic extrusion has made it a favored choice in various industries.
Real-world Applications and Effects of Plastic Extrusion
In the world of production, the method of plastic extrusion holds profound importance. The economic advantage of plastic extrusion, read this article mainly its cost-efficient and high-volume result, has revolutionized production. The market is persistently striving for technologies in recyclable and biodegradable materials, indicating a future where the advantages of plastic extrusion can be maintained without jeopardizing ecological sustainability.
Conclusion
Finally, plastic extrusion is a extremely effective and reliable technique of transforming raw materials into diverse products. It offers numerous advantages over other plastic forming techniques, including cost-effectiveness, high outcome, minimal waste, and design flexibility. Its impact is greatly really felt in various industries such as construction, automotive, and customer items, making it a critical procedure in today's production landscape.
Diving deeper right into the technological process of plastic extrusion, it starts with the choice of the suitable plastic material. As soon as cooled, the plastic is cut into the needed lengths or injury onto reels if the item is a plastic movie or sheet - plastic extrusion. Comparing Plastic Extrusion to Various Other Plastic Forming Approaches
Comprehending the types of plastic appropriate for extrusion leads the way for a wider conversation on exactly how plastic extrusion stacks up against other plastic forming approaches. Few other manufacturing processes can match the speed of plastic extrusion.